Dieselmotoren, vor allem die der aelteren Generationen sind eigentlich unverwuestlich. Ausrangiert werden sie aber alle meist aufgrund des gleichen Problems. Es gibt keine Ersatzteile mehr, vor allem für die vom Seewasser durchflossenen Teile der Kuehlung.
So hätte der Volvo Penta MD 21B unseres Bootes demnächst einen neuen Wärmetauscher und Ölkühler benötigt. Auch das seewassergekühlte
Abgassammelrohr war ziemlich angefressen. Der Ausfall der Wasserpumpe für den Primärkreislauf hätte mich 2010 auf den Azoren beinahe für längere Zeit festgenagelt. Für einen horrenden Preis konnte dann aber noch ein 30 Jahre altes Teil aufgetrieben und eingeflogen werden. Ersatzteile für den Basismotor zu bekommen (hier Peugeot 504) ist dagegen in der Regel kein großes Problem.
Nach über 30 Betriebsjahren und etwa 5 000 Betriebsstunden sollte die Maschine daher ausgetauscht und der gesamte Umbau in Eigenleistung durchgeführt werden.
Zunächst musste ein passendes Aggregat mit Getriebe für eine Wellenanlage ausgewählt werden. Da der Motorraum nur von vorn und von der Backbordseite zugänglich ist, wurde eine Maschine gesucht, die so wie der Volvo Penta MD 21B auf der Backbordseite die sogenannte Steuerseite hat. An Steuerbord, also an der festen Wand sollte der Abgaskanal angeordnet sein.
Des Weiteren sollte der Motor möglichst einfach
und robust aufgebaut sein, das heißt: kein Steuerriemen oder Steuerkette sondern Zahnradübertragung zur Nockenwelle, kein Turbolader, keine Steuerelektronik. Von der Leistung her durfte es gern etwas mehr sein, vom Gewicht her eher etwas weniger.
Nach Durchforstung des gesamten maritimen Marktes blieb tatsächlich ein einziger Motor übrig, der passte. Es war ein spanischer Sole Mini 62 mit 59 PS an der Welle und maximal 3000 U/min. Meine Begeisterung darüber hielt sich etwas in Grenzen, da der Motor in Deutschland kaum in großen Stückzahlen zur Anwendung kommt. Als Basis aber dient ein weltweit verbreiteter Mitsubishi Arbeitsmotor, der sicherlich als ausgereift zu bezeichnen ist. Standardmäßig werden dazu verschiedene Getriebekonfigurationen der italienischen Firma TwinDisc geliefert. Ich entschied mich für ein scheinbar gut dimensioniertes hydraulisches Getriebe Typ TM 345A mit einem um 8 Grad geneigtem Getriebeflansch.
Vorbereitung des Maschinenraumes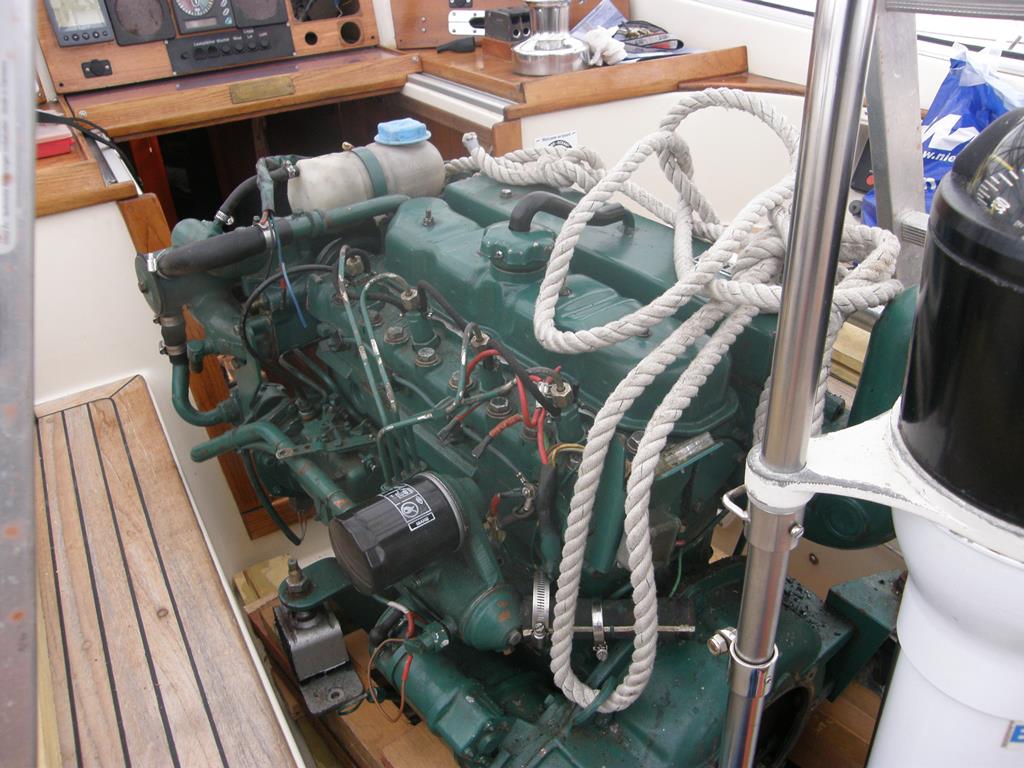
Im Zuge der Erneuerung sollte der gesamte Maschinenraum saniert werden. Zunächst wurde, nach Abklemmen aller Verbindungen, der alte Volvo herausgehoben. Er konnte später noch als Ersatzteilspender verkauft werden.
Des Weiteren wurde die im Motorraum befindliche Dieselheizung entfernt und später durch eine neue ersetzt. Auch die mit Öl und Schmutz verunreinigten Dämmplatten (insgesamt 7 m²) mussten erneuert werden. Gleiches galt für die Motorelektrik sowie für die Kraftstoff- und Kühlwasserschläuche.
Nachdem der Maschinenraum tatsächlich leer war, musste die alte Dämmung heraus genommen werden, eine ziemlich klebrige Angelegenheit. Weiter ging´s mit der Anpassung des Motorenfundaments. Es passte zwar vom seitlichen Abstand her, aber nicht von der Höhe. Gekürzt wurde es mit der Säge des Multimaster. Mit der Flex geht es zwar auch, der dabei entstehende Staub kann allerdings mit einem Pulverfeuerlöscher im Einsatz verglichen werden!
Um das Anpassen des Fundaments zu vereinf
achen, wurde ein Holzrahmen hergestellt und an der Unterseite des Rahmens die originalen Silentblöcke des neuen Motors im korrekten Abstand zueinander angeschraubt. Am Holzrahmen wurde außerdem im Winkel von 8 Grad ein Stück Besenstiel befestigt, der die Position der Propellerwelle abbilden sollte. Das war nötig, weil das Getriebe, wie oben beschrieben, mit einem 8 Grad geneigten Abgangsflansch geordert wurde und die Fundamentoberseite damit eine andere Neigung aufweist als das Stevenrohr (bzw. die Propellerwelle). Anschließend musste das Fundament im korrekten Winkel neu auflaminiert werden. Nach dem Aushärten, schleifen und spachteln, wurde das Fundament und auch gleich die Maschinenraumbilge mit Zweikomponentenfarbe gestrichen.
Jetzt konnte die neue Dämmung geklebt werden. Zum Einsatz kam ein Dämmstoff mit hohen Isolationswerten und abwaschbarer Oberfläche (Recygard W 1300 GA). Gegenüber einem Noppendämmstoff ist die Verarbeitung allerdings deutlich aufwändiger, da sämtliche Kanten zusätzlich mit Aluminiumklebeband abzukleben sind und sich das Material auch recht schwer schneiden lässt (Stichsäge mit Spezialblatt). Die silbrig glänzende Oberfläche macht den Maschinenraum aber hell und freundlich.
Motormontage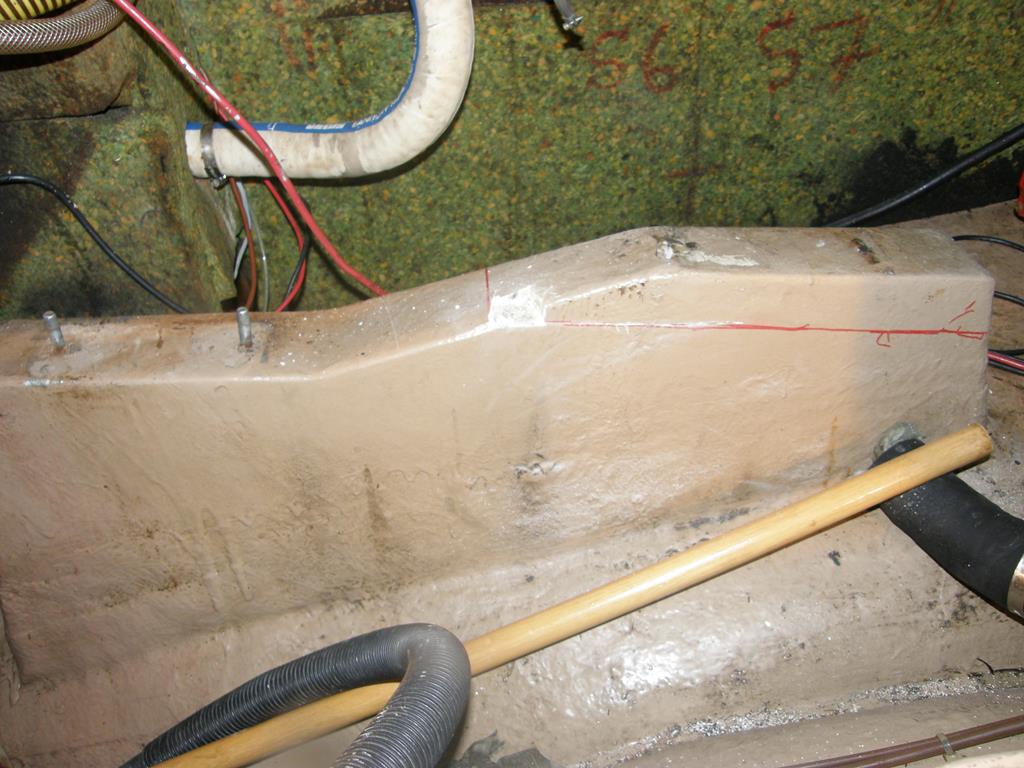
Nun konnte endlich das neue Aggregat durch die Montageluke im Plichtboden eingesetzt werden. Zur Befestigung des Motors auf dem Fundament wurden vier Stahlschuhe gebaut, die auch nach Montage des Motors noch in Längsrichtung verschoben werden können. Nach dem Ausrichten des Motors wurden sie später seitlich durchgebolzt und fest mit dem Fundament verbunden.
Das Anschließen des Motors gestaltete sich verblüffend einfach. Das Motorpaneel hat zwei patentierte Steckverbindungen, die einfach zusammengesteckt werden müssen. Das Plus-Kabel geht an den Anlasser und das Massekabel ans Motorgehäuse. Von der Verkabelung her war es das eigentlich schon. Will man zusätzlich einen Batterieseparator, Trenndiode oder ähnliches für eine weitere Batteriebank montieren, sind allerdings weitere Anschlussarbeiten notwendig.
Jetzt fehlen nur noch der Kühlwassereintrittsschlauch und der Abgasschlauch. Zum Schluss werden Dieselvor- und Rücklauf sowie ein entsprechender Dieselvorfilter angeschlossen. Letzterer wurde als umschaltbarer Doppelfilter beschafft und montiert, um beim Betrieb einen Sicherheitsvorteil zu haben.
Ausrichten des Motors zur Wellenanlage
Um einen möglichst ruhigen Lauf zu bekommen wurde auch eine flexible Kupplung (Bullflex 8) vorgesehen. Um den Getriebeflansch zum Wellenflansch aber wirklich exakt auszurichten, empfiehlt es sich einen starren Wellenflansch zu diesem Zweck zu besorgen. Die Gummidämpfer der Bullflex erlauben eine Ausric
htung auf maximal 0,05 mm, wie vom Getriebehersteller angegeben, nicht.
Probelauf
Endlich kam der Tag, auf den wochenlang hingearbeitet wurde. Öl und Kühlwasser wurden aufgefüllt und auch das Seekühlwassersystem war betriebsbereit. Die Kraftstoffleitungen wurden bis zur Einspritzpumpe entlüftet und der Zündschlüssel konnte das erste Mal gedreht werden. Nach der korrekten Vorglühphase sprang der Motor sofort an und lief ohne sichtbare Abgasentwicklung rund. Meine anfängliche Skepsis gegenüber der Maschine ließ allmählich nach.
Probefahrt
Die anschließende Probefahrt verlief allerdings sehr durchwachsen. Die Propellerwelle lief ohne sichtbare Vibrationen und der neue 3 Blatt Gori Faltpropeller brachte das 12 Tonnen schwere Schiff gut in Fahrt. Das Problem war nur ein deutlich hörbares Pfeifgeräusch, das nur bei Vorausfahrt zu hören war und mit zunehmender Drehzahl höher und vor allem lauter wurde. Es war so laut, dass es auch im Cockpit nicht nur zu hören war, sondern nach einer halbstündigen Fahrt regelrecht “auf die Nerven“ ging. Bei meiner sofortigen
Suche konnte als Quelle des Pfeiftons das hydraulische Getriebe vom Typ TM 345A ausgemacht werden. Ich tippte aus meiner Erfahrung heraus auf einen Lagerschaden.
Was ich zu diesem Zeitpunkt noch nicht wusste war, dass sich nun drei für mich sehr stressige Monate anschließen würden.
Ein Anruf beim Händler und dessen Rückfrage beim Großhändler in Holland ergab, dass man das eigentlich nicht nachvollziehen könne, da diese Getriebe ja alle einen Probelauf vor Verlassen des Werkes hinter sich hätten. Damit gab ich mich nicht zufrieden und bestand darauf, dass mein Händler sich vor Ort ein Bild vom Geräusch mache. Eine Woche später war es soweit, mein Händler und vermutete auch schnell einen Schaden im Getriebe. Da er vorsorglich schon ein Ersatzgetriebe mitgebracht hatte, wurde de
r Umbau sofort in Angriff genommen.
Eine weitere Probefahrt folgte im Anschluss. Festgestellen mussten wir dabei allerdings, dass das Pfeifgeräusch nach wie vor da war, in gleicher Höhe und gleicher Lautstärke. Was für ein Frust!
Mein Händler meinte daraufhin, dass das Geräusch nun ja wohl nicht mehr vom Getriebe kommen könne, da die Wahrscheinlichkeit, ein zweites defektes Getriebe erwischt zu haben doch ziemlich gering sei.
Fehlersuche
Nun hatte ich als Selbsteinbauer den schwarzen Peter in der Hand und meine verzweifelte Suche begann. Hinweise bekam ich von vielen Seiten. Singender Propeller, nicht korrekt ausgerichtete Welle, zu geringer Abstand vom Propeller zum Wellenlager, die Bullflex macht diese Geräusche, das Getriebe dreht falsch herum ... .
In wochenlanger Kleinarbeit bin ich fast jedem Hinweis nachgegangen, ohne den geringsten Erfolg. Der Chef der
Motorenwerkstatt unserer Marina hörte sich ebenfalls das Geräusch an und meinte, es komme vom Getriebe, was wiederum kein Wunder sei, denn die neueren leichten Getriebe mit Alugehäuse (25 kg) seien für so schwere Boote nicht wirklich geeignet. Sollte das stimmen? Warum gibt es dann aber keine entsprechenden Vorgaben vom Getriebehersteller? Nach Angabe meines Händlers ist das Getriebe selbst für deutlich größere Motoren ausgelegt.
Zu allem Überfluss musste ich nun feststellen, dass das Getriebe manchmal sehr verzögert schaltet, d.h. der Gang wird eingelegt und erst einige Sekunden später reagiert das Getriebe auf den Schaltbefehl.
Die ersten 50 Betriebsstunden des Getriebes waren zwischenzeitlich um und es waren die ersten Ölwechsel bei Motor und Getriebe fällig. Während der Ölwechsel beim Motor wie erwartet ohne Befund verlief, war das beim Getriebe nicht der Fall. Das Getriebeöl war sehr dunkelgrau und der Magnetfilter voller metallischem Abrieb.
Nach dem Ölwechsel reagierte das Getriebe zunächst überhaupt nicht auf Schaltbefehle. Musste hier etwas entlüftet werden? In der Anleitung gab es dazu keine Hinweise. Nach einig
em Probieren ging´s wieder.
Bilder vom Öl und vom Abrieb sendete ich nun an meinen Händler, verbunden mit dem Hinweis auf sich häufende Schaltprobleme. Ich bestand nun auf einen weiteren Getriebetausch, da der Sommerurlaub bevor stand und ich in Schweden nicht irgendwo liegen bleiben wollte. Wir vereinbarten, für den Tausch möglichst ein kräftigeres Getriebe zu ordern. Das ebenfalls hydraulische Getriebe TM 93A ist vorwiegend für die Berufsschifffahrt vorgesehen, wiegt 52 kg und hat ein Gehäuse aus Gusseisen. Von den Maßen her ist es wenige Zentimeter länger und breiter, sollte wohl aber passen.
Ein weiterer vom Holländischen Großhändler bestellter Fachmann kam an Bord und checkte das Getriebe. Auch er kam zum gleichen Schluss. Das Getriebe musste ausgewechselt werden. Da mein Urlaub näher rückte und ich noch keine Rückmeldung bekommen hatte, schrieb ich den Großhändler selbst an und machte auf meinen Zeitdruck aufmerksam. Ein
en Tag später bekam ich einen Rückruf aus Holland. Nach kurzer Diskussion ging man auf meine Forderung ein und ich bekam gegen Zahlung der Differenz beider Getriebe das größere TM 93A zugesandt. Man sagte mir, den Ölkühler könne ich vom alten Getriebe weiter nutzen.
Den erneuten Umbau musste ich natürlich in Eigenregie übernehmen. Mit zwei Helfern gingen wir zwei Tage vor Urlaubsstart den Umbau an. Jetzt sollte wirklich alles klappen. Erste Schlappe: die Hydraulikleitungen zum/vom Ölkühler passten nicht ans neue Getriebe. In der Stadt gab es zum Glück eine Hydraulikwerkstatt, die mir sofort Schläuche in richtiger Größe konfektionierte.
Der Flansch (aus 12 mm Stahl) des neuen Getriebes passte zum Glück korrekt auf die Glocke des Motors. Auch die sechs Bohrungen sind an der richtigen Stelle. Nach Anschrauben des Flansches ans Getriebe mussten wir allerdings feststellen, dass drei der sechs Bohrungen vom Getriebegehäuse verdeckt wurden und damit für die Befestigung am Motor nicht nutzbar waren. Irgendetwas passte da nicht. Ein weiterer Anruf bei meinem Händler war fällig. Dass da nur drei Schrauben genutzt werden können, sei bekannt und leider nicht zu ändern, es sei wohl ein Universalflansch, der auch an anderen Getrieben passen solle. Das Ganze hielte aber auch mit drei S
chrauben, so sein Fazit.
Uns gefiel das gar nicht und wir machten uns die Mühe, zwei weitere Bohrungen in den Flansch zu setzen und zwei M 10 Gewinde in die Glocke des Motors zu schneiden.
Wieder musste der Motor neu ausgerichtet werden. Am Ende des zweiten Tages war endlich alles fertig, Öl aufgefüllt, der Bowdenzug angeschlossen und wir konnten den Motor zum finalen Probelauf des Getriebes starten. Was für eine Anspannung!
Fehler gefunden
Nach dem Einkuppeln in Vorausrichtung fehlte tatsächlich das so nervige Geräusch und das Boot nahm ruhig und zivilisiert Fahrt auf. Was für ein Genuss nach all dem Stress!
Einen Tag später begann der Urlaub und ich war wirklich URLAUBSREIF!
Fazit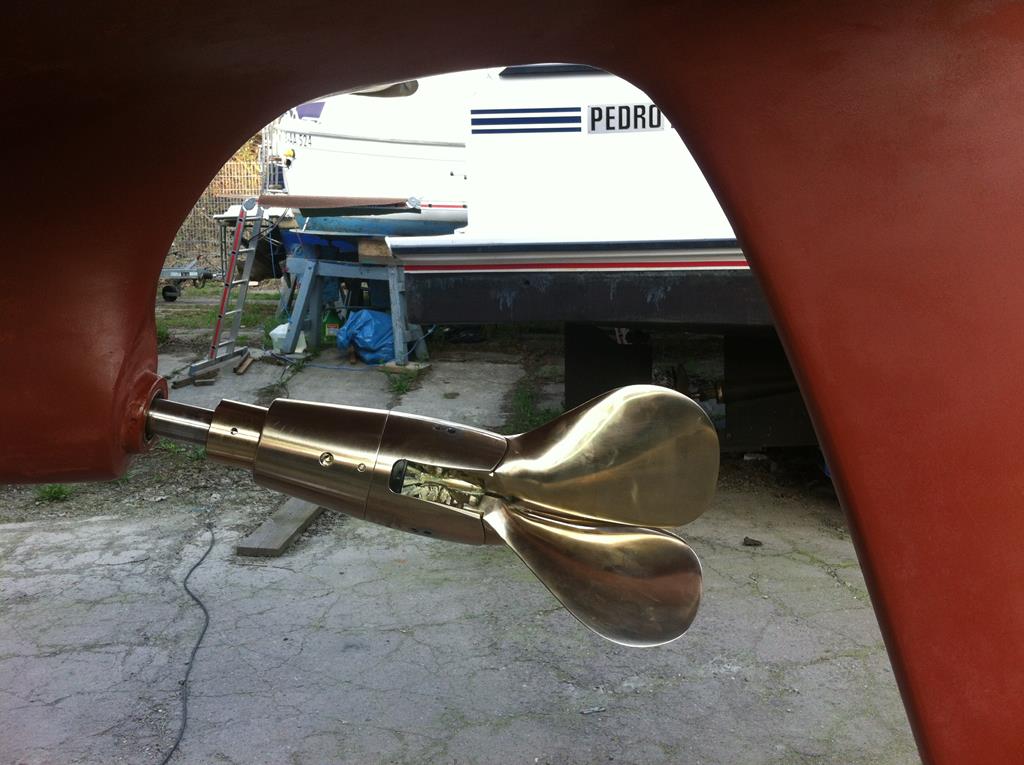
Als Selbsteinbauer hat man alle Risiken, die sich aus der gewählten Kombination ergeben, beginnend vom Motor bis hin zum Propeller selbst zu tragen. Händler und Großhändler haben bei der Problemlösung unterstützt, die richtige Lösung zu finden und dann auch umzusetzen, bleibt aber Aufgabe desjenigen, der die Technik einbaut.
Der stressärmere aber eben auch deutlich teurere Weg wäre die Vergabe der Installationsarbeiten an eine geeignete Firma. Man sollte vorher genau abschätzen, ob man sich diese Arbeiten, auch beim Auftreten potentieller Komplikationen zutraut.
Bei der Getriebeauswahl ist scheinbar nicht nur die zu übertragende Leistung sondern auch der Druck auf das Drucklager des Getriebes zu berücksichtigen, der linear zur Verdrängung des Bootes zunimmt. Eine andere Lösung wäre der Einbau eines externen Drucklagers, die Umbauten dafür wären aber ungleichhöher gewesen.
Torsten Gräser (Text und Fotos), SY Taras